Supply Chain Quality Risk Management - SCQR
simplifying SCQ Risk
Supply Chain Quality and Risk Management all starts with an effective process. Our approach starts with a thorough review of the markets you operate in, and are likely to operate in, to understand the regulatory requirements for your product range. We then perform a risk assessment on the product range and the supplier / country of manufacture to develop a risk matrix meaning you focus you QA/QC budget on where it needs to be spent.
When the policy is documented, we can then help cascade to your internal and external stakeholders, meaning all are aware of the policy and framework approach, a critical step in ensuring a smooth program is delivered.
The next step is to perform vendor / factory audits & assessments as well as implementing an incoming material control approach. This helps validate that the process controls are in place to deliver good quality, safe products. The validate stage is the core inspection and test program, this will vary based on the risk matrix findings and your own risk aversion approach.
Finally, we provide quarterly management briefings where we assess performance within the supply chain, look to improve the program where it makes sense and ultimately evolve the policy to meet the changing requirements of the market.
After all this, the end goal is a program that continually evolves and improves supply chain performance. One whereby the best in class vendors get rewarded (eg, skip lot inspections) and where the returns due to poor quality and recalls are mitigated. The end result is an improved bottom line and a brand that is protected.
Product Validation Product Quality Control Inspection Program Development 2nd/3rd Party QC Audit/ Inspection
Advance Quality Planning Risk Audits/ Gap Analysis Failure and Effects Analysis Production Part Approval
Solution
Testing

In today’s highly complex and changing marketplace, finished product suppliers, buyers and manufacturers need to be confident that the products they deliver to market meet consumer expectations along with the required safety, environmental, regulatory and government standards globally. The need to meet these objectives is crucial. Non-compliant products risk being recalled. Poor quality products can result in consumer dissatisfaction and product returns. Both can negatively impact brand image.
Working with major international retailers and brands, helping shape the standards and regulations through participation in industry forums and regulatory agencies and with labs in every major selling and sourcing country, we provide a comprehensive testing services for a very broad range of products throughout the supply chain.
• Quality / Performance Testing
• Safety Testing
• Reliability Testing
• Environmental Performance Testing
• EMC Testing
Testing is an important component of managing quality assurance throughout your supply chain. The testing process begins with understanding the product from your point-of-view. Where will the product be marketed? Who will use the product? What are your quality expectations?
The answers help identify the regulatory and quality standards for your product – and consequently the appropriate testing so you can sell, manufacture, or distribute your product anywhere in the world with confidence
Inspection

With decreasing product life cycle and time-to-market, the challenge to deliver quality products on-time increases. If a product is found not to meet the appropriate quality specifications for the marketplace – either after or late in the production stage – the result can be loss of product and revenues, delayed shipment or wasted materials, and the potential risk of a product recall.
A third party inspection is the verification of product quality to pre-identified quality specifications before, during and/or after the production process. Prior to the manufacturing process, raw materials can be inspected to identify if the materials themselves meet specifications. During the manufacturing process, products are inspected at the factory to verify that quality requirements and specifications are being met. After production, goods can be inspected prior to loading and unloading to verify that the approved final product is shipped and received according to the buyer’s requirements. Inspections throughout the various stages of production can help both buyers and manufacturers monitor that quality requirements for the product are being met and support on-time delivery of quality products.
A third party inspection program can assist your company to:
1. Strengthen and protect your brand image and reputation
2. Improve performance of suppliers and product quality to minimize the risk of product loss, rejects, charge backs and recalls
3. Drive continued improvement of quality systems and performance to benefit both the buyer and producer
4. Protect sales revenue by helping to prevent late shipments, poor quality, wasted materials or empty shelves
Auditing

An audit is a systematic evidence gathering process. Non-financial audits of systems and processes involve periodic verifications to verify that a documented QHSE management system or industrial process is being effectively implemented.
They help validate compliance with regulatory requirements and industry standards. Audits can also be used as an information tool to drive better business decisions.
Verify compliance and make informed business decisions
Riebdon provides a range of auditing services to support businesses in quality, health and safety, social compliance and environmental management. These audits can form part of certification requirements, or be carried out independently to support specific business needs.
Our audits range in scope, from a consumer goods factory capability and capacity assessment, to one-off technical audits as part of a construction project, or verification of a commercial transaction, to a complete audit of a global quality management system on behalf of an industrial or consumer goods manufacturer.
Riebdon auditors can confirm compliance, for example with workplace health & safety regulations. They can also identify ways to assess product quality or improve performance, for example in the case of building energy audits.
Regular audits can be used as a tool for continuous improvement, or to drive change throughout the business. Our supplier and network auditing programs, for example, help businesses ensure their suppliers adhere to specific quality and social standards and processes.
-
Factory Assessment Solutions
-
Social Compliance Solutions
-
Precious Metals Audit
-
Storage Facility Auditing
Factory Assessments
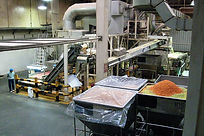
In today’s highly competitive consumer market, buyers need a vendor base that will partner with them to meet all aspects of production, from design and quality to product life cycle times and delivery requirements. However, how do you effectively select new partners? How do you monitor the progress of existing vendors? And how can you effectively work with vendors to keep the focus on quality as well as time?
A factory assessment audits the production capability and performance of a factory against proven quality principles. As such, the key criteria assessed are policies, procedures and records that would indicate the factory’s ability to deliver consistent quality management over time, rather than at one given time or only for certain products. Core areas and processes addressed by a factory assessment include:
• Quality Management System
• Good Manufacturing Practice (Factory Environment Standards)
• Product Control
• Process Control
• Personnel
Key Benefits:
• Evaluate capabilities of potential new vendors as part of the selection process
• Identify key strengths and weaknesses of your existing vendor base
• Monitor and track progress over time to drive quality throughout the manufacturing process
• Provide an independent assessment tool that retailers, buyers and vendors can use together to make improvements
Consultancy and Advisory

Whether you need to understand regulatory requirements, insight into a failure, improve a product, enhance communication among your partners in the supply chain, or source products more efficiently from multiple vendors, our Advisory service offering provides customized recommendations for you.
Our team provides a broad spectrum of consulting, engineering and analytical services to aid and support companies with the complex questions and issues that arise in today's global supply chain environment. It also represents a full range of knowledge and experience in such areas as manufacturing, quality assurance, industrial technology, mechanical engineering, operations management, business development, and product design.
Key Challenges we can support you with include product development guidance, brand protection, sourcing solutions, reduction in time to market and customer satisfaction.
Key Benefits:
• The answer or solution for your specific concern or question
• Improved communications and processes throughout your supply chain
• Simplified vendor/factory selection process
• Reduced costs and sourcing lead times
• Enhanced risk management and brand protection
Supply Chain White Paper
Click to Open >
Request a Quote
To get a better idea of how we can provide you with this service, fill in the quotation form. We will contact you.
Let US Help
If there's any way we can help, please let us know.
407.494.5191
> Submit an Inquiry Form